比钢铁更坚硬更轻量的纳米纤维
日本的研究团队开发出了可高效制造以木材为原料的坚硬轻量环保型新原材料“纳米纤维”的技术。
木材的每一个细胞都被细胞壁包围着。该细胞壁的构造与钢筋混凝土相同。相当于混凝土的是被称为木素的高分子,相当于钢筋的则是纤维素。将该纤维素解开并进行重组的是纤维素纳米纤维(CNF)。纤维素占据细胞壁的大半成分,因此木材中含有丰富的纤维素。
近年来,CNF制造技术的开发竞争越来越激烈。主要理由是,CNF的重量仅为钢铁的五分之一,却拥有约钢铁5倍的强度。只要将CNF与塑料树脂混合,就可制造出轻量坚硬的复合材料。
汽车和家电等产品使用塑料和合成纤维等多种化学品。化学品的主要原料为石油,约占日本石油消费量的23%。若可转换为利用CNF加强化学品的复合材料,不但能够减少石油消费量,而且还能够实现产品轻量化,从而有助于减少CO2排放。
以汽车为例,如果将约占车体重量9%(约110kg)的塑料树脂建材更换为CNF强化树脂,可实现约20kg的轻量化,并可期待耗油量的大幅减少。
对日本的产业来说,最有希望的是,可有效利用木材这种天然资源。日本的很多资源都依赖于海外进口,但木材是国内为数不多的可量产的资源。日本的森林约占国土的7成,在发达国家中属最高水平。
在这种背景下,举国推进研究开发的时机越来越成熟了。政府在今年6月通过内阁会议决定的《日本复兴战略2016》中明确记述了“CNF的国际标准化和面向产品化的研究开发”。另外,经济产业省也提出了“在2020年实现CNF量产化,在2030年实现相关市场规模年1兆日元”的目标。
但是,在将CNF和塑料树脂混合之前,还需要很多工程,因此CNF强化树脂的价格高达1万日元/1kg,制造成本越来越高。如何通过有效方法制造高质量CNF,是研究课题之一。
在这种情况下,今年3月,在新能源・产业技术综合开发机构(NEDO)的项目中,以京都大学为主体的产学合作团体将制造成本控制为目前成本的十分之一,成功开发出了从原料的木材屑到CNF强化树脂复合材料,一气呵成制造出的方法(京都进程)。
为控制成本,京都进程导入的制法之一是“化学变性”。在传统制法中,在实施“纳米化”-将作为原料的纸浆分解为纳米大小的纤维后,需要再进行化学处理,具有易与塑料树脂混合的性质。
NEDO材料・超精密加工技术部的佐佐木健一说:“很多树脂都具有与油相近的性质。而CNF与水的亲和性却很强。油性和水性物质即使混合,与色拉油同样,也无法相互渗透。”
为解决这个课题,研究队伍实现了通过化学处理使CNF接近油性的化学变性,从而有助于工程的简略化。并且,采用了对纸浆进行化学变性后实施纳米化,然后与树脂混合的工程。这是因为如在进行化学变性前实施纳米化,之后的工程将变得困难。
京都进程中产生的CNF特点之一是,留下适度木素的“Ligno CNF”。世界上的研究者认为不需要木素,想要制造无木素的CNF。但是,如去除木素,就会出现伤到纤维素,耐热性也不会提高的课题。京都进程反而留下木素,从而成功制造出耐热性强的CNF。
佐佐木健一说:“今后我们将向多个企业和官方机构提供‘京都进程’中制造的CNF样品,反映用户心声,加快实用化的步伐。”
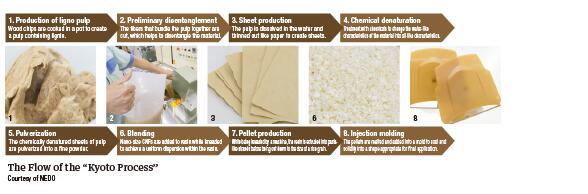
|